3D Printing’s Greatest Achievement, NASA Creates Rocket Engine Injector
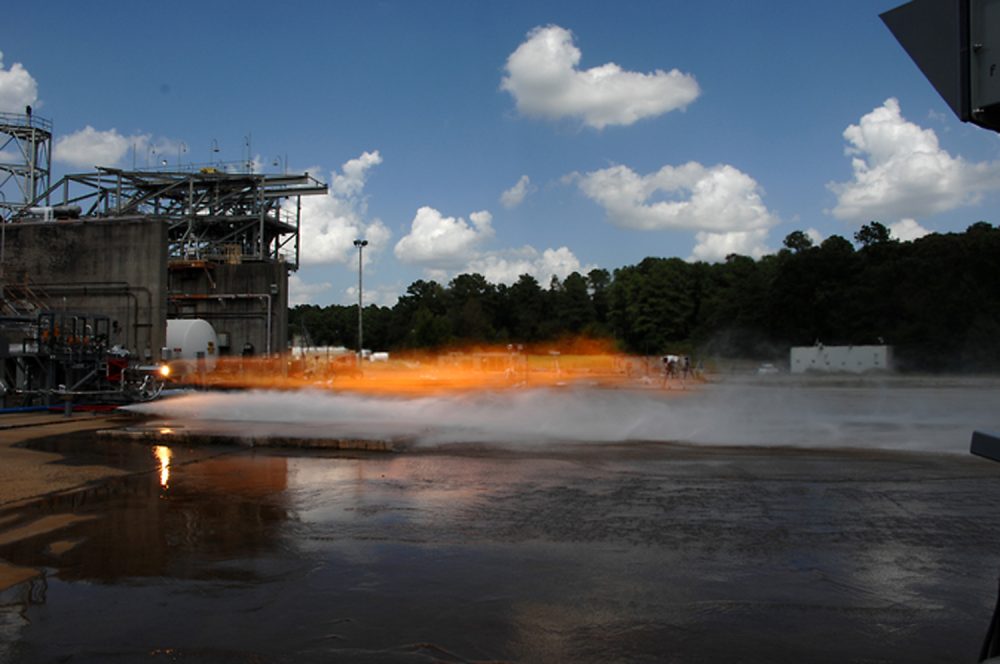
3D printing is one of the most beneficial technologies out there and it is all set to bring immense comfort to our lives in the coming decades. It is a process through which one can create three-dimensional objects in which successive layers of material are laid down under computer control. NASA pushed the limits of this technology and decided to create one of the most complex parts of a rocket engine, and then they tested the prototype. What happened next will blow your mind.
At a test stand at NASA’s Marshall Space Flight Center in Huntsville, Alabama, scientist tested out a design with a new manufacturing process. The design was fed into the computer and then manufactured layer by layer in a 3D printer. The process involved layering metal powder and fusing it together with a laser, a process known as selective laser melting.
This injector design was similar to the ones that are used in small rocket engines. It is also close to the design of the RS-25 engine which will power the Space Launch System (SLS), which will be the biggest rocket ever built. The entire injector was created as a single component instead of manufacturing each element individually. In traditional processes, about 163 individual parts are made and then assembled for this extremely complex equiment. This process is economical, both money and time wise.
NASA engineers tested out two designs for five seconds each, and they produced 20,000 pounds of thrust. They performed as per the expectations. The 3D printing process afforded the engineers the convenience of building parts that enhance the performance of the rocket engine. They created geometric flow patterns that allowed oxygen and hydrogen to swirl together before combusting at 1,400 pounds per square inch and temperatures up to 6,000 degrees Fahrenheit.
For this initiative, NASA took the assistance of two private companies, Solid Concepts in Valencia, California, and Directed Manufacturing in Austin, Texas. Both companies were responsible for printing out one injector for testing.
NASA now plans to test out the feasibility of additive manufacturing process in the entire manufacturing process of a rocket engine. They have already tried complex injectors and other components through 3D printing process, and are impressed by the speed at which the components are manufactured and the ease of testing these components. The technology will make space travel a lot more convenient too. Instead of taking huge cargo of equipments, astronauts can simply print out the tools they need, thereby being independent of the earth base. 3D printing, by the looks of it, is here to stay, and this technology is capable of changing the world.